This post may not be super revolutionary but it can get you out of a jamb or at least save some money. For me, I am typically paying $60-$100 a gallon. To top it off, getting rid of leftover paint is also a pain. In my state, every container is charged a recycling fee. That is supposed to cover the cost of returning leftover paint for recycling.
A quick word about recycling. There is a company in the state that picks up all of the paint that is returned. Everything is sorted, for instance exterior and interior and by color. Then like colors are grouped together and mixed and finally standardized into a basic color palette to be sold at a value price.
I have personally never used the paint, so I cannot really comment on the performance or quality. I would consider it for applications that do not have high performance applications like interior paint or outbuildings that you just want to get something on. There is a lot of science involved in paint and just combining different manufacturers could effect the integrity of the paint.
Back when I was a youth and working with my grandfather, we would occasionally gather all of the leftover paint and mix it together. Often times, it would come out as a brown or olive color (as exterior). Interior whites were a no brainer, you ended up with some shade of white that was unique but just fine.
When you have multiple buildings to maintain, a smarter tactic is to standardize on one color. Many times we did use the same color, but there were times when it was inconvenient to drive across town to buy paint or a tenant had a special request or we were given paint and other such random events. Consequently, we always had a mishmash of paint.
I talked about this subject last year on July 1, 2020 when I referenced the color ‘Pandemic Pink’. That was a mixture of a lot of my random exterior colors that came out pink. Today I am going to mix leftover interior paint for my sheetrock priming. My plan is to mix about 1/2 a quart of yellowish/orangish with about 1/2 a gallon of purplish gray with one gallon of PVA drywall sealer. I expect it will come out as a light brown.
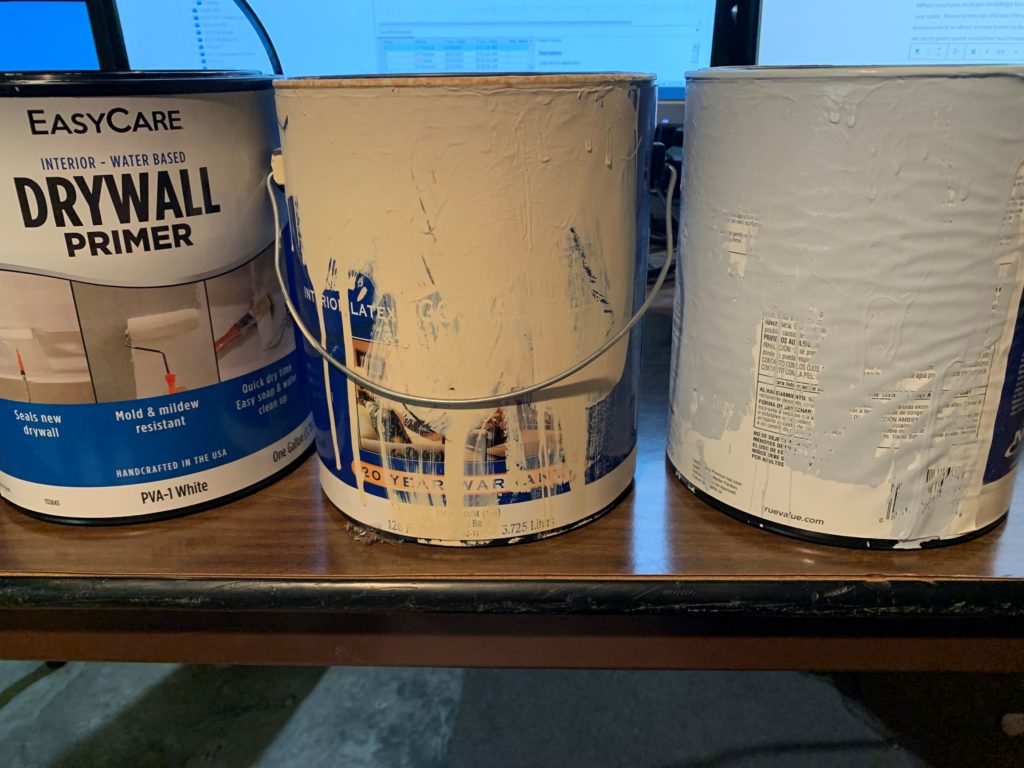
Ultimately, I am going to paint over it with something whitish because I want as much light as possible in the room. I just haven’t totally decided yet because I want to minimize the inventory of leftover paint. I also want to minimize cost so I am weighing total cost versus future utility.
Additionally, I wont go as far as saying paint has a shelf life but in practical terms nothing lasts forever. What I have found is that the container fails before the the paint actually goes bad. The ammonia used to buffer the paint (water-based) rusts steel and causes pinholes to let air in and dry out the paint. My point is that if you are saving partials for eventual touch-up you may find that your partial is no longer paint some day when you open the container.
End Your Programming Routine: As I mentioned above, there is a lot of science to paint. I am going to end it here today and save getting more detailed into the qualities of paint later. If you have a bunch of paint that you no longer need or want and a project that needs some painting, consider recycling it yourself.
Recent Comments