I haven’t even brought this up, but I have quietly working on another sofa table. My wife wanted to steal the one I made for my office the minute I brought it into the house. I promised that I would make her one and I finally got around to it. It had to come after the summer projects but we are now into the shop time of year.
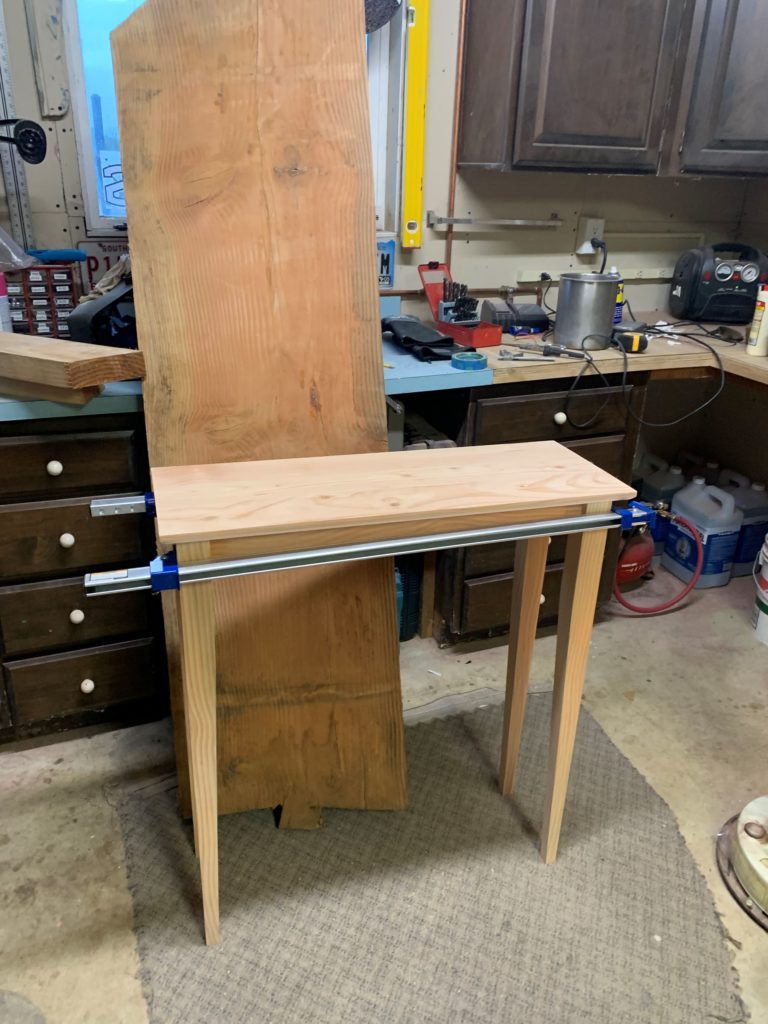
As a very infrequent woodworker, I am lucky if I get one project done let alone the chance to duplicate a project I have already done once. This was an opportunity to really see if the reason it took so long to build the first one was my problem or it was really that difficult. I knew the answer, but I still wanted to see how fast I could do it. This picture was two weeks after I had drawn up the plans.
As it stands in this picture, this is about 20 hours of work. This includes drawing the design out on graph paper and picking out the boards from the stack. So, it is definitely my problem. I find myself falling into the trap that I don’t have time to do this or that and so things drag on months and months. When I am most productive, I say to myself either ‘I have to get this done today’ or ‘I have thirty minutes, how far can I go?’.
Back when we lived in South Carolina, my wife wanted a mantel built by Christmas. It was about 4AM Christmas day that I finished. I really don’t recommend that kind of effort unless this is your career or have nothing better to do in life but other’s having deadlines is also a good way to not end up flaking out on a project either.
I did have some help on this one that I didn’t have before. I used the taper jig that I built for the first table and I have about the same height of legs. Instead of chiseling out the mortises by hand, I just cut them with the router this time. The first time, I wanted desperately to prove to myself that I had the knowledge to do fine woodworking. This time, I took the pragmatic approach that I had nothing to prove and that was a much faster way to do things. Practicing is a sure way to do things much faster than the first time.
I almost used pocket screws instead of mortise and tenon joinery. That would have knocked at least four hours off of my time. I didn’t think the joinery was actually necessary but I thought that the practice would be good for me. I also think in the end, it made a better final product. By better I mean that the joinery was more likely to stand the test of time then screws. Everyone that has ever had Ikea furniture knows that the first move is when things start to go south in the durability department.
At first my wife was wanting different legs and I thought that I was going to get an opportunity to buy a wood lathe. As much as I would have loved to add that to my tool collection and skills, I convinced her that duplicating the shaker style legs I used on my first table was the fastest way to get this project done. I have other things in the queue besides this table, not to mention my long anticipated wine cellar.
End Your Programming Routine: My Toolbox Fallacy is real. ‘I can’t do this, until I do/get that’. Sometimes I figure out that I bought stain in a color that I already have or I already have the sandpaper. Then I figure out that the thing I was using as my excuse to not do something was there all along and I really had no reason not to work on projects. I am happy with the results and I feel even better that I learned things that really helped me with this table. On to the next project.
Recent Comments