At some point, I am going to write an article about dealing with siding penetrations and other unforeseen problems. To be effective, I would like to have pictures (or video) to go along with it. Since I do not have that yet, it definitely doesn’t make sense to do today.
In lieu of actual content, I will fill space with worthless words (just kidding). I am on the mend, no fever the last couple of days and energy feels good. I still have junk in the throat but the show must go on. Monday, I got back to work and in two hours I had all of the siding off. Yesterday’s goal was to cut the compromised drywall and remove portions of the panels.
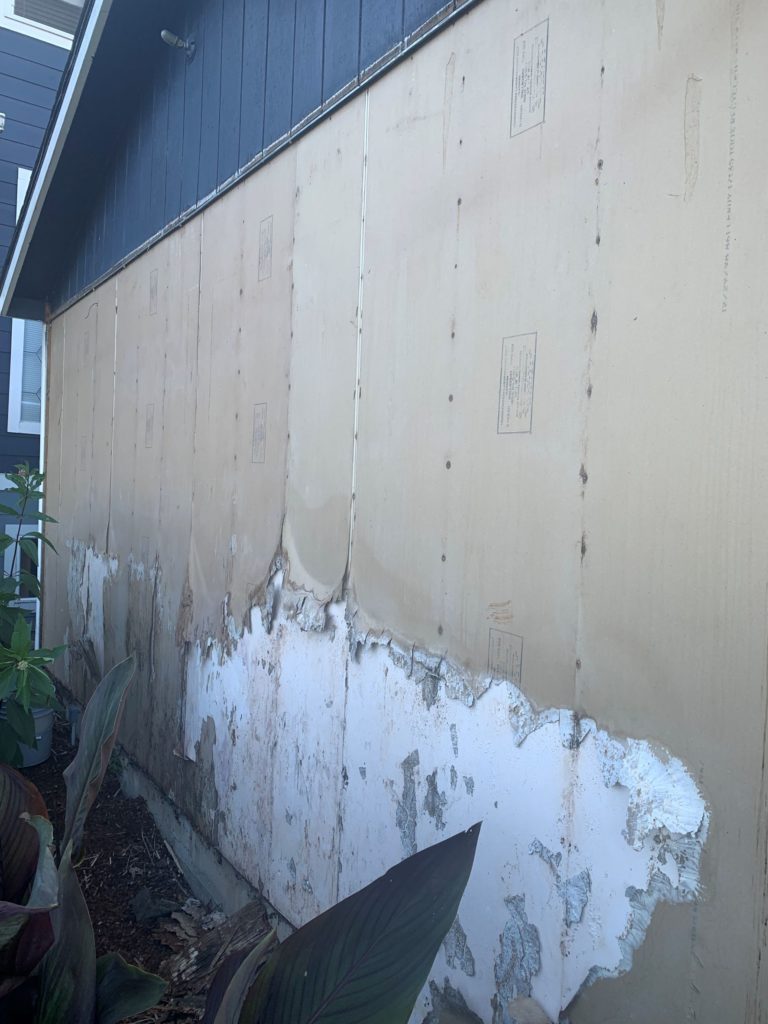
I cut the bottom four feet off the offending panels. That should allow me to slap up new ones with the minimum of cuts. After that, I am going to add a Water Resistant Barrier (WRB in the lingo) which will actually be tar paper because that is what I have.
The key to fixing this failure is the details. Normally, T1-11 would not necessarily need a WRB between the panel and the sheetrock. But, because the HardiPlank was applied over the T1-11, water went between the two and stayed wet for an extended time which in turn rotted the T1-11 behind the lap siding. Proper products and flashing will resolve this permanently.
Before I do this, I have a couple of reservations. The first is I am not completely convinced that fire protection (the purpose of the drywall) is necessary. When nailing the HardiPlank back on, the only way to secure it is nailing through the studs. I have inspected the corner construction and there is no structure to nail the edges of the siding. This has me thinking that I should change the backing from drywall to sheathing.
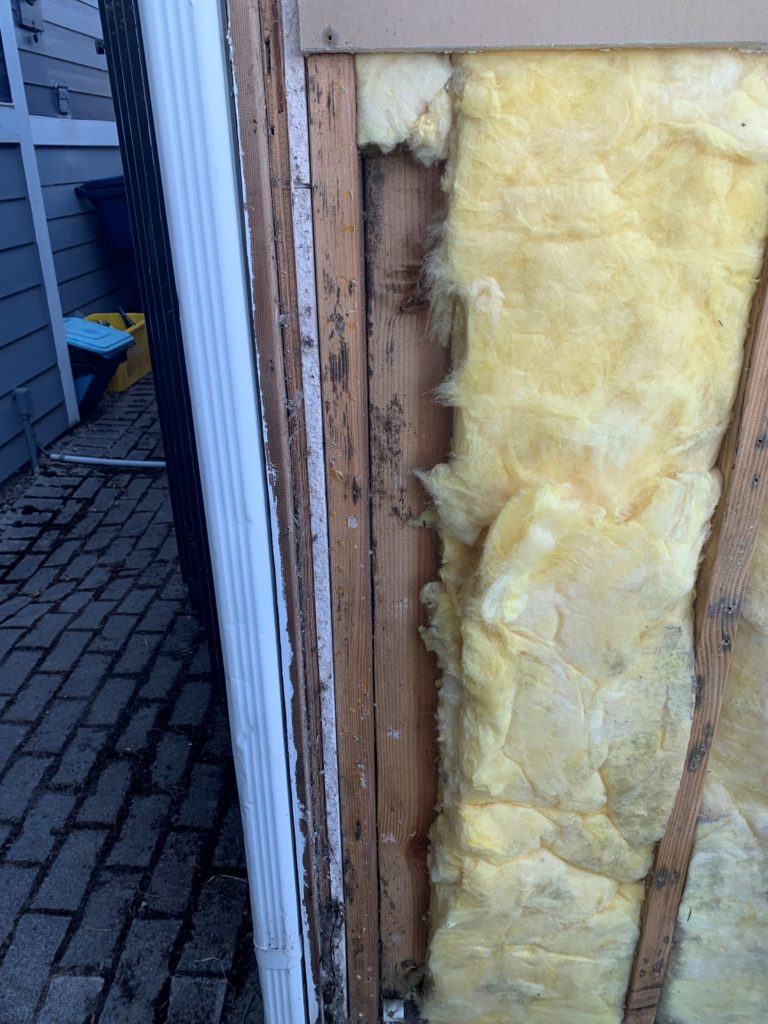
Looking at the cost between OSB and drywall, they are nearly the same. And, HardiPlank is also fireproof. It will be the structure for nailing the lap that will help me decided how to proceed.
End Your Programming Routine: When this garage was built, I think it was done properly. I am pretty sure the lap siding was added later which is why the details were wrong. Or, at least that is what I want to tell myself. I guess we will all see as I go along, stay tuned for the proper way of doing things.
Recent Comments