I am trying to figure out where to go from here. It is increasingly difficult to prioritize the time to write, balance family time with work and accomplish all the other tasks that need to get done in life. More specifically, to what end? I didn’t start this because I was bored in life, I started to try and build a career replacement.
Maybe I didn’t use my time as effectively as I could have when I had it. I certainly was slow to get my domain started and branch out. I am not aggressive about the business aspects. The truth is, I have discovered that I really don’t want to participate in social media. I find the interaction a chore and somewhat detestable.
I guess that I would compare social media to shopping at Costco. Many people I know like to shop at Costco. There are some nice things about it, but high on my list is consistency of availability. I never know if what I want is available. I never know if what I want to see on social media is available and I don’t want to spend my time ‘shopping’ just to see.
Just like other social media, my branding has been a little all over the place. I suppose what I was trying to accomplish was interweaving life with skills. I have not been consistent with my delivery of good skills based content and have wandered quite a bit, particularly since I finished my remodel. I am making no promises here, but since I have a project going on, I should take advantage of the fact.
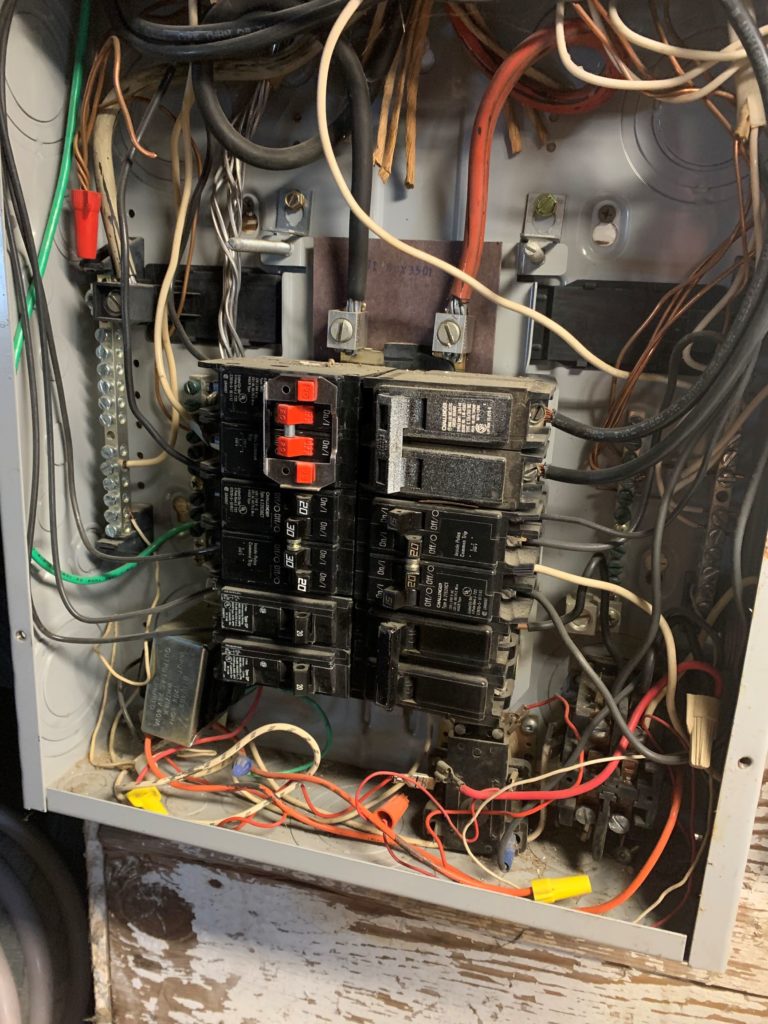
Since I spend a lot of my workday being cold, getting heat is a priority. I was looking at my subpanel trying to figure out what the unmarked breakers were and what space I had available. The upper left 20A 240V breaker was wired to a baseboard heater that is no longer installed and the target of my interest. But further to that, why did I have so many 240V breakers?
I found that I had one 20A 240V breakers un-used and one 30A 240V breaker empty. On top of that, there was some curious wiring. One leg of the bottom right 20A 240V circuit was tied to a relay and two 12V transformers that didn’t go anywhere. My speculation is that this has been an electrical free for all.
The DC wiring I think was for an internal vacuum system but I really don’t know. There is also heat tracing on all of the piping in the basement has not been connected since I have lived here. Maybe that is the reason? I was going to cleanup everything, but ultimately I decided to disconnect and remove all of the low voltage stuff. I have lived here over sixteen years and never knew or needed it, it is not likely I was going to miss it.
So, I have my circuit for my heater and I have space to add an office specific 20A circuit and I simplified my panel. I have built my Bill of Materials and made my cost estimate. It is almost time to really get started.
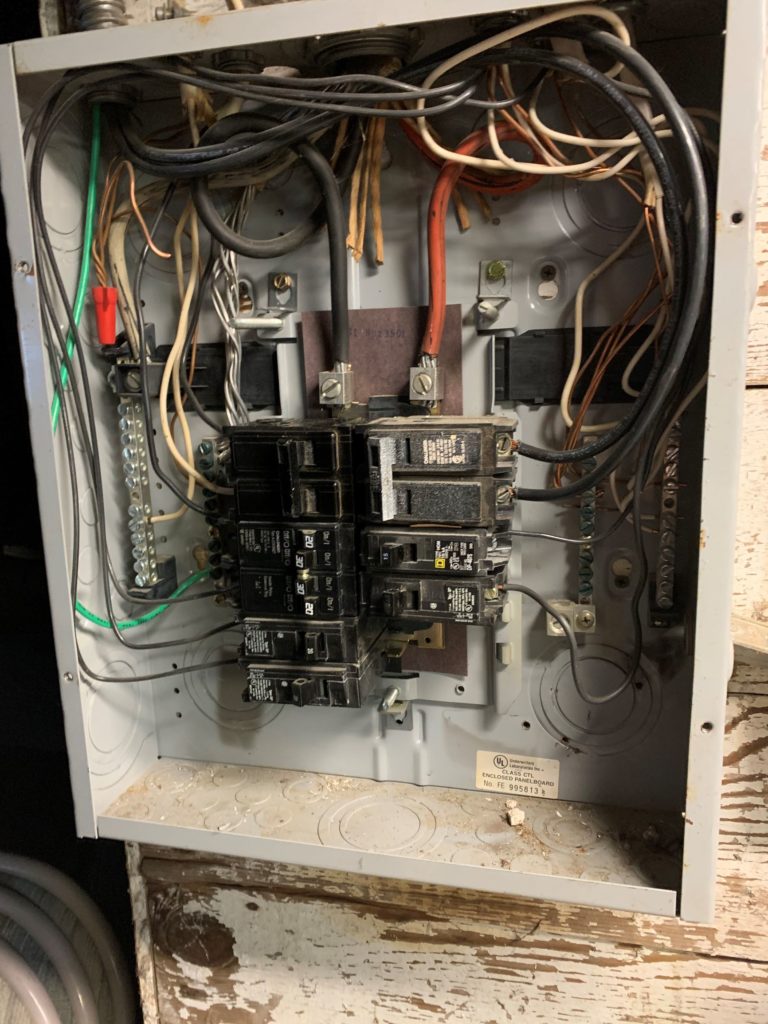
Recent Comments