I have to vent for a minute. I have a garage for a reason. Not only should I be able to park a car in it which it was until the Mustang was sold, but I should also have a place to work on cars out of the weather. That I cannot do. Secretly, I can barely stand to go into the garage because it is so cluttered.
I have been needing to do the brakes on the pickup for a while. It was something I was planning on doing when the weather was nicer. You all know how my summer went and it didn’t get done. I mentioned to my wife that the needed to be done and she immediately helped me prioritize the job.
I should mention that this was not an emergent problem. One of the rotors was warped which caused a terrible vibration. If things are going well, like not metal on metal contact, I am in the habit of just changing the pads. It is faster and cheaper. But, something must have happened since I didn’t change the brakes that long ago (in milage). I have been putting up with it for several years but I drive fairly gingerly. Now that my son is the primary driver of the pickup it was time to do it.
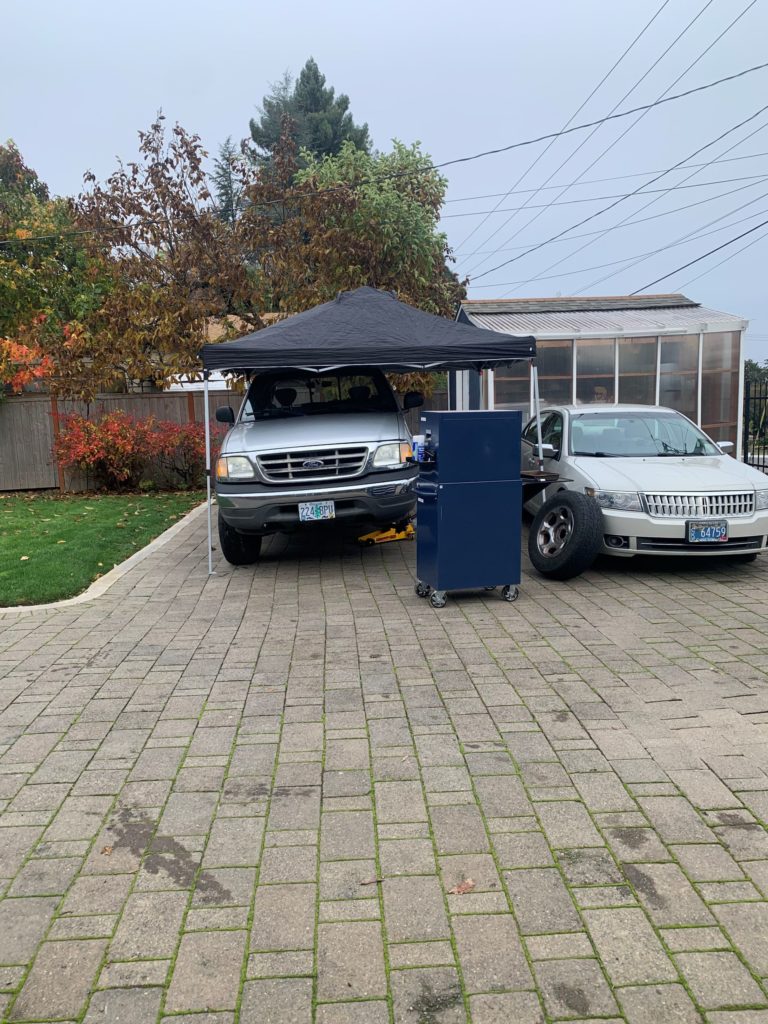
My wife was at a girl’s weekend and I didn’t have to work. I was dreaming of all the things that I wish I was doing besides freezing my hands with cold metal. Worse than that, rain was in the forecast I had no garage. Plus, I was on the clock with only eight hours of daylight. I had a few tasks to do that day including adding the cargo carrier to the Navigator, replacing a taillight lens plus removing the canopy from the pickup.
I devised that I was not going to beat the weather so I had better set up a work space where I could get the job done. I took the time to setup a popup, organize the parts and tools and make my workspace as comfortable as possible. That included a bucket for a seat and the radio for the football game.
After about thirty minutes, the rain started coming down in buckets. As my weather luck was turning bad, so was the football game. It was a miserable time for shade tree mechanics and Beaver’s fans. The total job took me about four hours. I had to go back and forth to find my tools that my son has taken out of my tool box, find the right sockets and the proper tubing for the brake bleed.
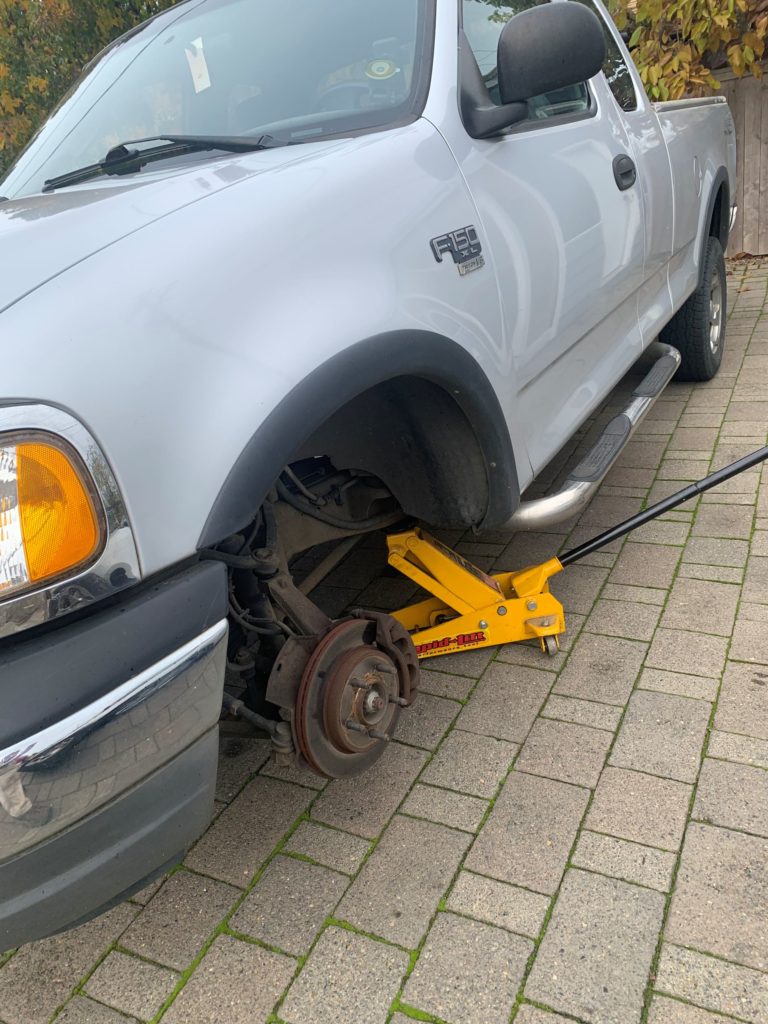
A recent brake job at a tire store cost me $750. I was travelling for work and my wife was on a road trip with the kids so it was kind of an emergency. Mind you, I had just paid a mechanic for the same job about two months earlier and I was not happy in the least. I paid about $120 for parts for this job. And I got a $30 rebate to boot that I am waiting for.
Over the years, I think that I have made almost every mistake under the sun doing this job. This includes twice having the bolt holding the calipers on fall out. When that happens, the bracket bangs against the wheel making a heck of a racket and impossible to drive without feeling like major damage was about to happen.
I now know to use thread locker and torque the bolts to the right amount so it won’t happen again, I hope. Experience helps with expediency and proficiency. I think most people with the tools, the space and mechanical aptitude could do it too. I realize that is some major hurdles for some but why have all the stuff and not do it?
End Your Programming Routine: I am glad it is done and despite everything I very well may have saved time but definitely money. Even with bleeding the brakes it is not that difficult of a job. It was more that I just didn’t want to be out in the elements. I am convinced that I could probably do this in half the time if I didn’t have to spend time messing with the popup and setup. I was tired and sore and happy to be inside a warm, dry bed by the time it was over.
Recent Comments